Optical Emission Interferometry (OEI) in the Plasma-Therm Versaline PECVD
Overview
In plasma-enhanced chemical vapour deposition (PECVD) tools, the deposition rate of deposited films can often fluctuate with relative gas concentrations, material build-up on the chamber walls, and other mechanisms that make timed depositions inconsistent. To combat this problem, a simple technique called Optical Emission Interferometry (OEI) can be used. OEI provides a more robust form of deposition control based on the interference of light reflected off of the growing film to precisely hit target film thicknesses.
OEI uses similar principles to other interferometric tools like the Filmetrics F50-UV; the intensity of light at a single wavelength reflected off of a thin film will vary depending on the wavelength of light and the optical thickness of the film. This is due to the relative phase difference between light reflected off the top surface of the film and at the film-substrate interface, i.e., conditions of constructive and destructive interference (shown in Fig. 1). Across a broad spectrum of wavelengths, this can be used to fit to both refractive index and film thickness robustly (as Filmetrics does). However, if the intensity of light reflected off of a growing film is recorded continuously, the intensity at a "single" wavelength will oscillate approximately sinusoidally as the thickness increases (satisfying constructive and destructive interference conditions at specific thicknesses)—this is the fundamental premise of OEI. By noting when the extrema occur during film growth, the period of this oscillation (T) can be used to measure the deposition rate of the film, since T is set by the phase conditions for constructive/destructive interference. T = λ/(2n); where λ is the wavelength of interest and n is the refractive index of the material at this wavelength.
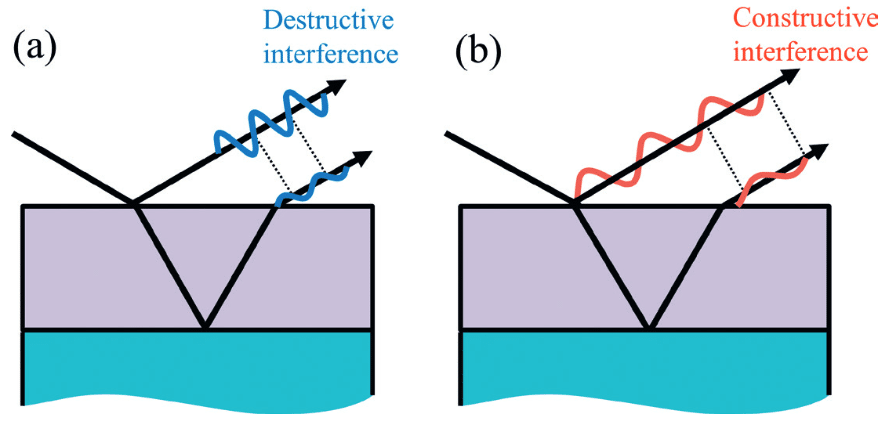
To use OEI in the Plasma-Therm Versaline PECVD, light produced by the plasma is reflected off of the growing film and collected by a spectrometer centred above the wafer for plasma monitoring. The Plasma-Therm EndpointWorks software package is then used to monitor the evolution in time of the spectral intensity emitted from the plasma within a narrow range of wavelengths. Choosing a range that encompasses an emission line of a typical gas/radical species within the plasma produces the oscillatory data shown in Fig. 2. Values of T are calculated based on known values of n and λ to give an estimate of the deposition rate based on the spacing of the extrema. Thus, in order to function correctly, each OEI recipe requires the user to have knowledge of both the growing film (single wavelength refractive index) and of typical optical emission lines (usable wavelengths) within the plasma.
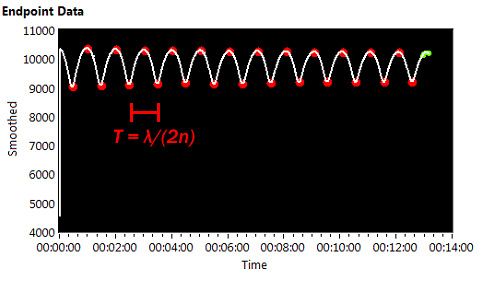
Wavelength choice
The choice of what wavelength to use for OEI depends on the chemistry of the plasma in question, since each gas/radical species emits light at different wavelengths (depending on its electronic transitions), and thus the available wavelengths will differ for each recipe. Potential emission lines are further limited if the gas species characteristic of an emission line is consumed during the reaction. The intensity of these reactant emission lines will fluctuate as the film grows and as the local gas concentration changes. In contrast, the intensity of an emission line of an inert gas (He, Ar, or N2 are often used to dilute the reactants) will be much more stable, and will provide a reduction in noise in the reflected light. This leads to a more clearly defined periodic signal, where the extrema can be easily identified in software. Additionally, since variation in T is linear with the wavelength of light used, the choice of shorter wavelengths will reduce the period of oscillation, lending the OEI method more sensitivity and flexibility to accurately measure thinner films. Note, for films that are optically absorbing (e.g. a-Si and Si-rich nitrides), the film will absorb more strongly at shorter wavelengths, decreasing the amplitude of the oscillation as the film grows. Ultimately, this decay reaches a point where extrema cannot be identified past a certain thickness. A general rule of thumb is to choose the shortest wavelength inert gas emission line that is not strongly absorbed by the depositing film. A typical spectrum collected during deposition is shown in Fig. 3, where a N2 emission line at ~333 nm is highlighted, being suitable for the gas chemistry involved. For more details on choosing an emission line appropriate for your deposition, please see the Plasma-Therm Versaline PECVD OEI recipe development How-To on the nanoFAB's Confluence Knowledge Base.
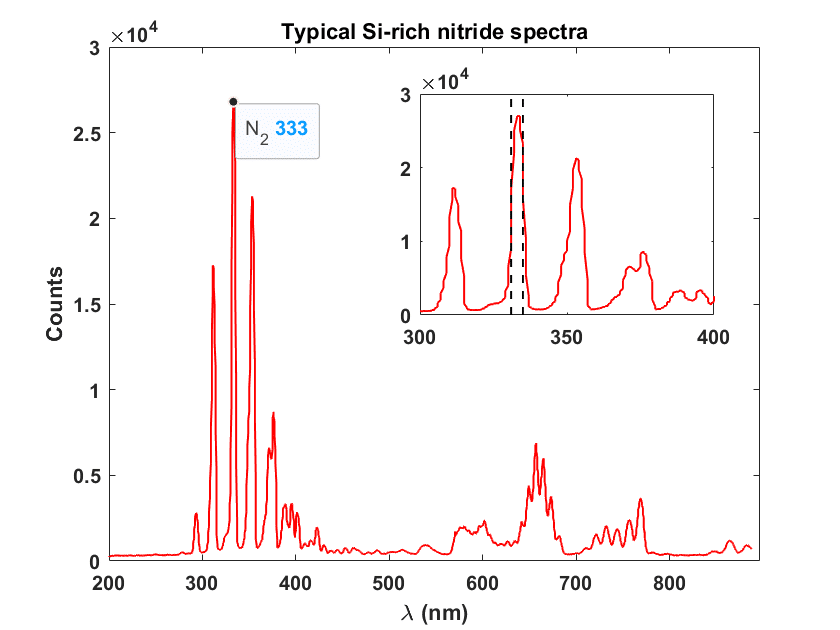
OEI controlled deposition recipes are currently qualified for SiO2 Dep ("OEI SiO2 Dep") and Stoichiometric Nitride ("OEI Stoichiometric Nitride") recipes, with an OEI recipe in progress for the Si-Rich Nitride. For user-developed films that differ from these established recipes, users are welcome to qualify their own OEI recipes following the Step-by-step instructions in the linked OEI recipe development How-To. If you encounter problems setting up your OEI recipe on EndpointWorks, please contact Tim Harrison (tr1@ualberta.ca).