AML Wafer Bonder now available for training
The nanoFAB is pleased to announce an upgrade to our wafer bonding and packaging area, with the recent installation of a wafer bonder from Applied Microengineering Ltd (AML). The AWB-04 wafer aligner-bonder from AML offers a wide range of bonding techniques and process flexibility. Of particular note is its in situ alignment capability, allowing users to verify correct alignment as the wafers are being brought into contact.
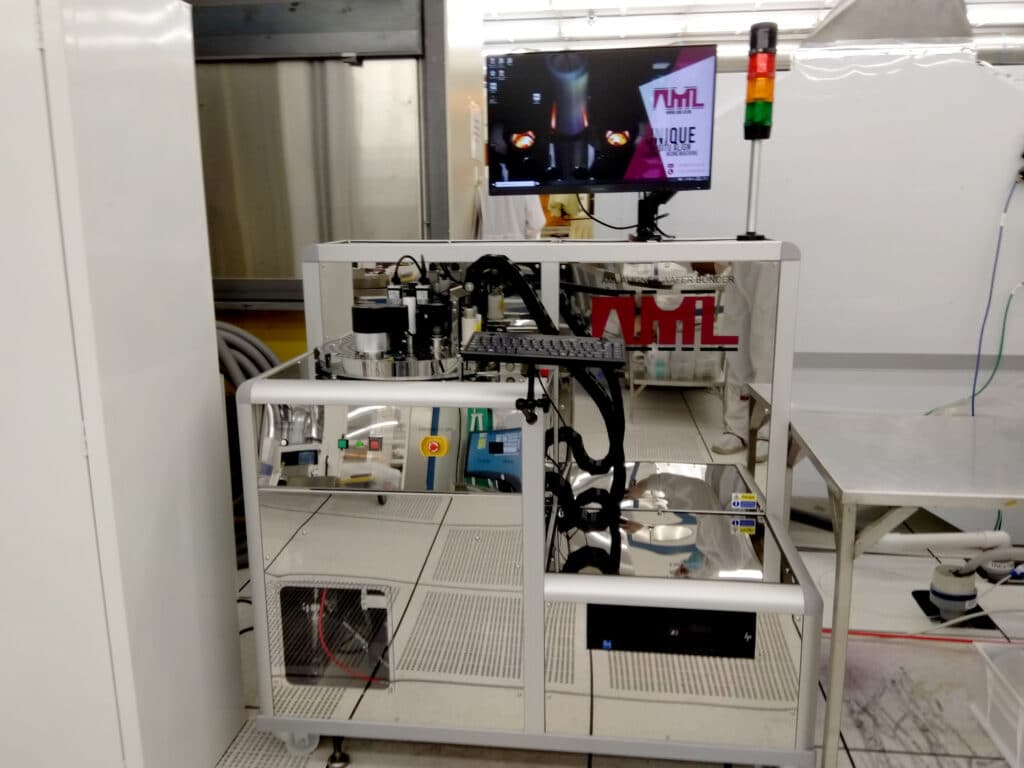
Bonding techniques include:
- Anodic (borosilicate glass to Si)
- Direct (Si to Si)
- Eutectic (Si to Si or Si to glass with intermediate metal layer)
- Thermocompression (bonding between metal films deposited on both substrates)
- Other custom bonding techniques
Technical features:
- Up to 150 mm wafer sizes (100 mm and 150 mm hardware available)
- In situ alignment (visible and IR) with 1 µm accuracy; manual and automatic (image recognition) alignment procedures available
- High vacuum (10-6 Torr)
- Wafer separation of 30 mm
- Independent platen temperature control, up to 560 °C
- Radical activation (RAD) for in situ surface cleaning and activation
- Bonding forces up to 40 kN
- Anodic bonding voltages up to 2.5 kV, current limits up to 8 mA
- Triple-stack anodic bonding
- Wafer edge clamping (no contact on bonding surfaces)
Application Examples
Anodic Bond: borosilicate glass to Si
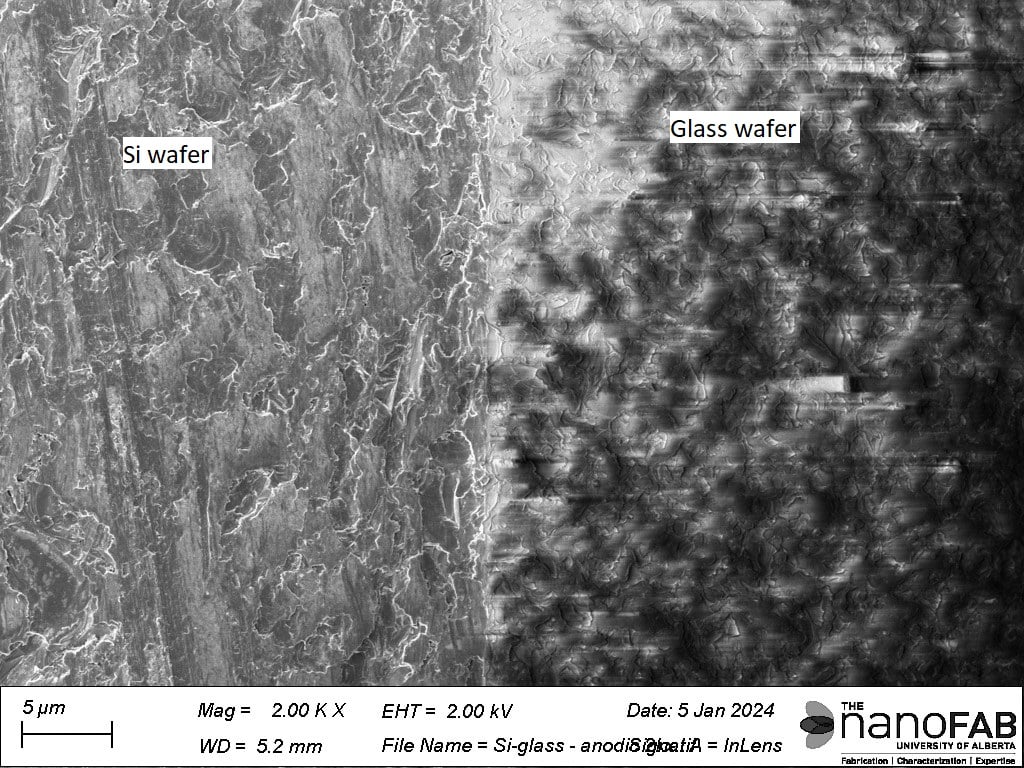
Si–Si Direct Bond: in situ RAD + low-temperature anneal
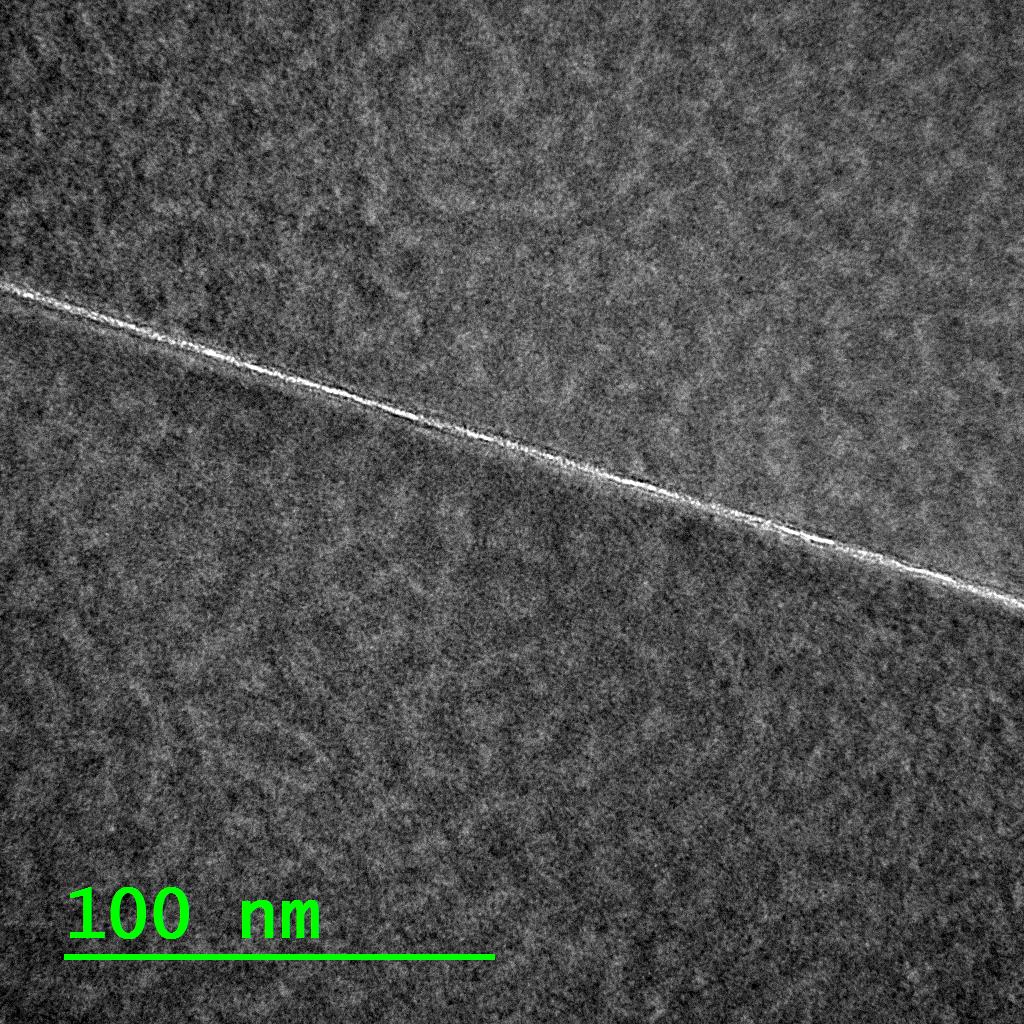
Si–Si Direct Bond: in situ RAD + external high-temperature anneal
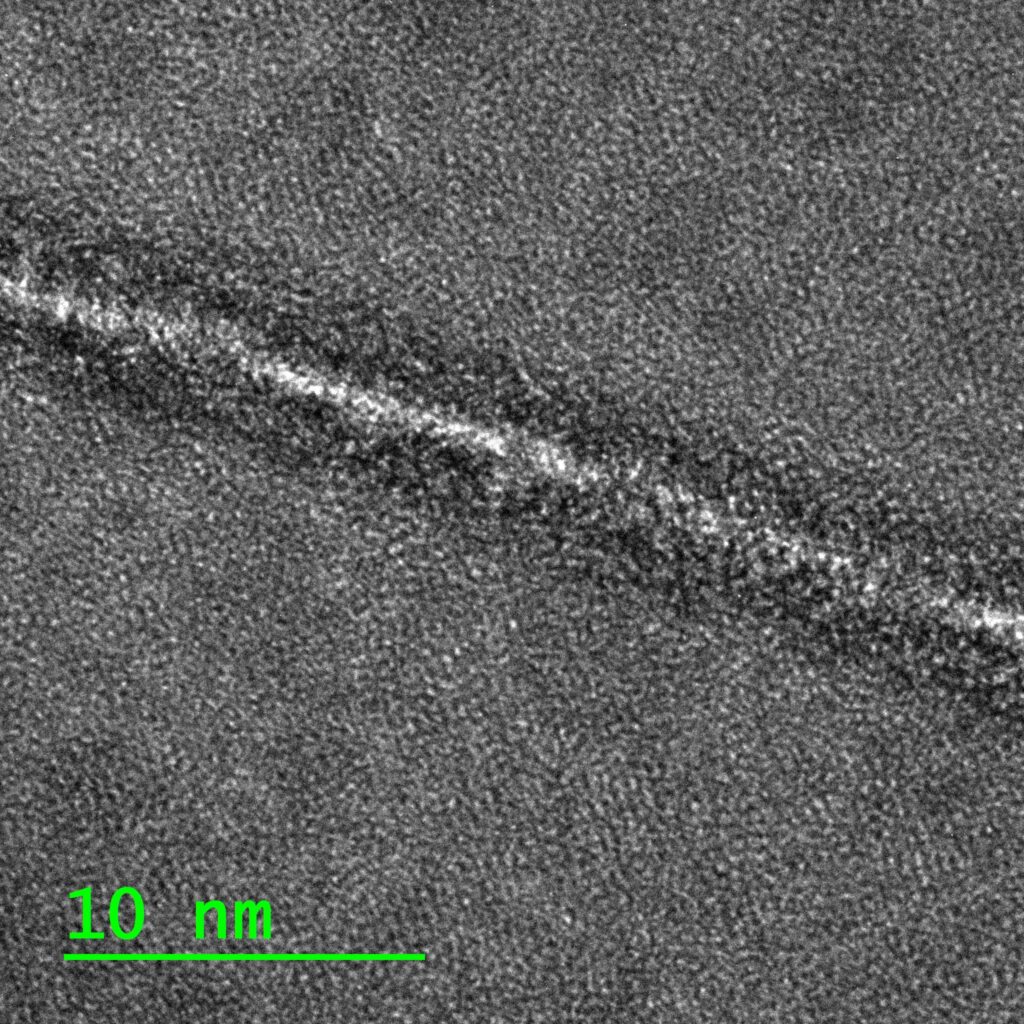
Au–Au Thermocompression Bond: Si to Si with Au interlayers
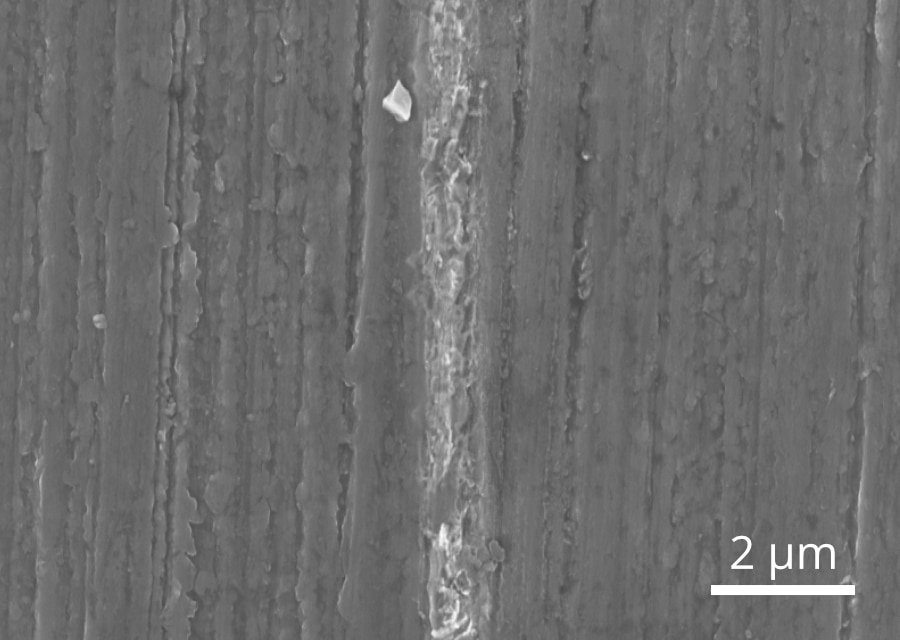
If you are interested in using the AML wafer bonder in your work, please submit a request through LMACS to receive training. If you have any questions, please feel free to contact Scott Munro or Aaron Hryciw.